GENERAL
GMP Manufacturing in Pharmaceutical Production: Prioritizing Safety and Efficacy
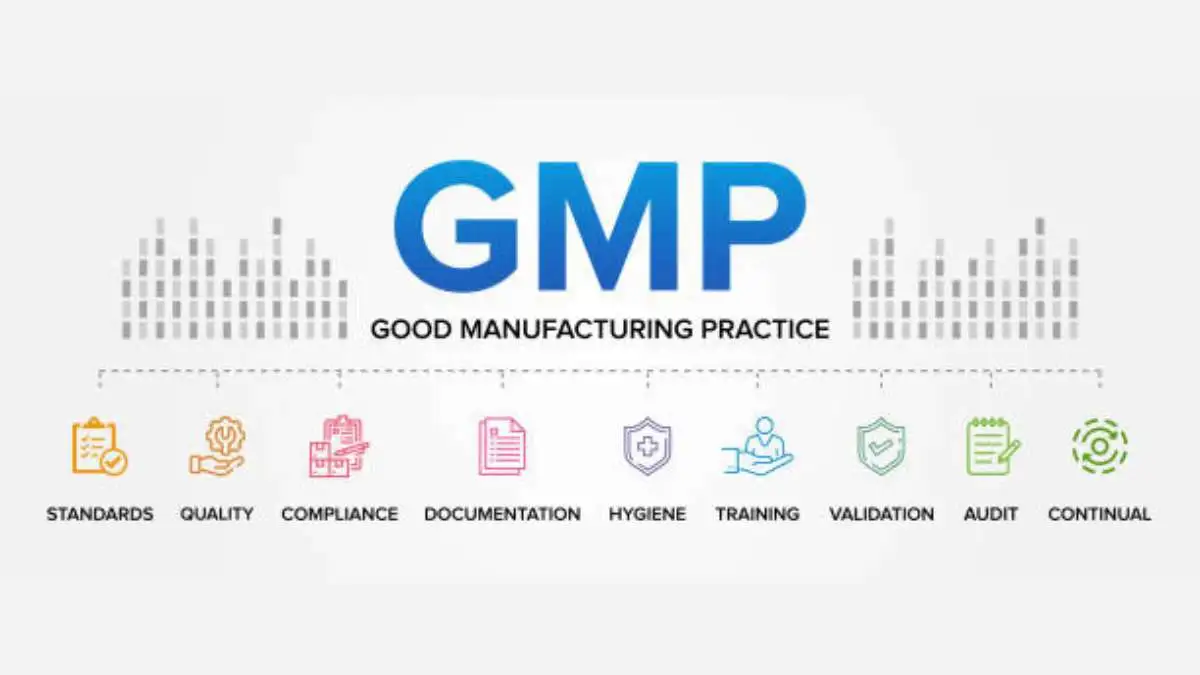
Introduction to GMP Manufacturing
Good Manufacturing Practice (GMP) is a strict system that guarantees pharmaceutical products are consistently made and monitored in line with predetermined quality standards. This practice is particularly crucial in the pharmaceutical industry, where GMP manufacturing serves as the backbone of drug production, fostering the creation of medications that ensure patient safety and therapeutic efficacy. By strictly adhering to GMP guidelines, pharmaceutical companies can produce high-quality drugs that meet both industry and regulatory standards, providing the desired therapeutic effects for patients and minimizing risks associated with drug contamination and incorrect formulations.
The foundational principles of GMP are designed to minimize the risks involved in pharmaceutical production, addressing issues that cannot be fully mitigated through final product testing alone. By implementing these principles, manufacturers ensure a controlled and clean environment conducive to consistent, high-quality drug production. This proactive approach not only safeguards consumer health but also enhances product reliability, thereby bolstering pharmaceutical manufacturers’ overall credibility and trustworthiness.
Table of Contents
Key Elements of GMP in Pharmaceuticals
Pharmaceutical manufacturing processes must adhere to stringent regulations to ensure the quality and safety of the medications. These detailed instructions address different aspects of production to make sure each step helps achieve the ultimate objective of producing safe and effective pharmaceuticals. Crucial components consist of:
- Proper facility design and maintenance: Facilities must be built and kept up in a way that makes cleaning and sanitizing easy. This layout reduces the chance of contamination and provides a controlled setting that is ideal for producing high-quality items.
- Use of validated equipment: All equipment used in the production process must be regularly calibrated and validated. This ensures consistent performance and accuracy, which are critical for maintaining product quality.
- Standard operating procedures (SOPs): Detailed, written procedures for all processes that impact product quality must be developed and followed meticulously. These SOPs provide a clear framework for operations, ensuring consistency and reliability in production.

- Quality management systems: Robust quality management systems, including comprehensive documentation and regular audits, help maintain high-quality production standards. These systems ensure that any deviations are quickly identified and corrected.
- Employee training and hygiene: Staff must receive adequate training to perform their duties while adhering to high levels of personal hygiene. Proper training ensures that all employees understand and follow GMP guidelines, reducing the risk of errors and contamination.
The Role of GMP in Ensuring Drug Safety
GMP manufacturing is paramount in ensuring the safety of pharmaceutical products and implementing rigorous testing and validation at every stage of production. This meticulous process significantly reduces the risks of contamination, mix-ups, and production errors. Adherence to GMP guidelines enables companies to produce consistently safe products that protect consumers’ health.
Companies that comply with these standards gain regulatory approval and can market their products confidently. The meticulous nature of GMP practices ensures that any anomaly during production is promptly identified and rectified, preventing unsafe products from reaching the market and thereby enhancing consumer safety and trust.
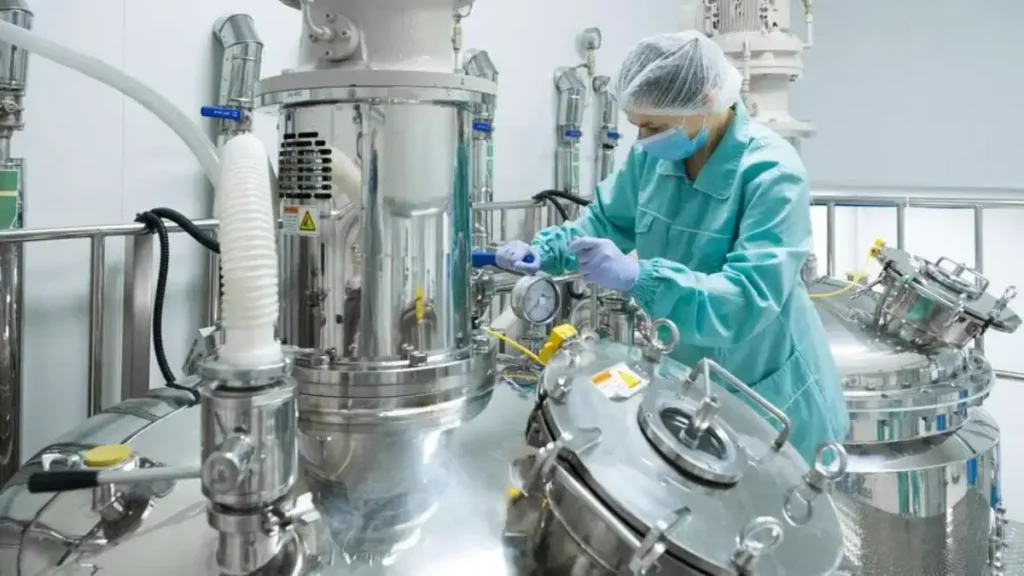
Enhancing Drug Efficacy through GMP
GMP practices play a crucial role in ensuring that pharmaceutical products are not only safe but also effective for their intended uses. By meticulously controlling every aspect of the manufacturing process, GMP helps uphold the potency and stability of medications. This includes precise measurement of active ingredients, maintaining optimal storage conditions, and conducting stringent quality checks at various production stages.
Effective medications are essential for treating health conditions and improving patient outcomes. Reliable drug efficacy boosts patient confidence and adherence to prescribed treatments, ultimately contributing to better public health. By adhering to GMP standards, pharmaceutical companies can ensure that their products deliver the intended therapeutic effects, reinforcing the importance of GMP in maintaining high-quality healthcare solutions.
Challenges in Implementing GMP
Despite its critical importance, implementing GMP principles can pose significant challenges for pharmaceutical companies, particularly smaller firms. The high costs associated with establishing and maintaining GMP-compliant facilities and equipment can be prohibitive. Additionally, the need for specialized training programs to ensure staff competency in GMP practices is both time-consuming and costly.
Navigating the complex web of regulations governing GMP can also be daunting, requiring companies to undergo regular and thorough inspections to achieve and maintain compliance. Despite these challenges, the investment in GMP practices is invaluable, ensuring the production of high-quality, safe, and effective pharmaceutical products. Companies that prioritize GMP compliance are more likely to succeed in gaining regulatory approval and maintaining consumer trust, ultimately driving their long-term success in the competitive pharmaceutical market.
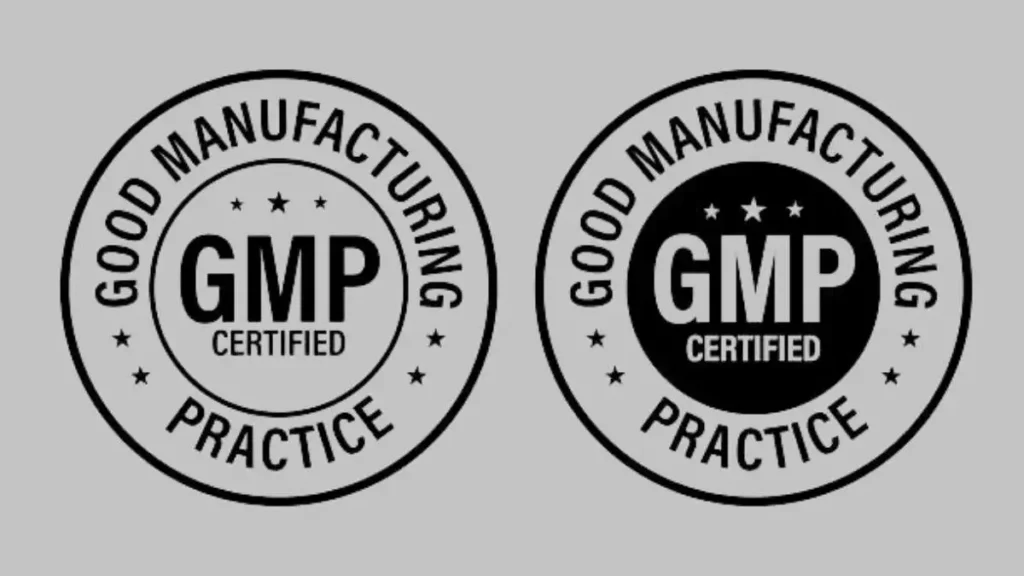
Future Trends in GMP Manufacturing
With the advancement of technology, the methods and procedures for GMP manufacturing in the pharmaceutical sector are also developing. Automation and data analytics are being more and more incorporated into GMP procedures to improve efficiency, precision, and trustworthiness. For instance, automated systems can continuously monitor production environments, ensuring consistent conditions and minimizing the risk of human error.
Innovative approaches such as continuous manufacturing—where production processes are streamlined into a single, uninterrupted flow—are set to revolutionize the pharmaceutical landscape, providing more efficient and cost-effective production models. Furthermore, the rise of personalized medicine, which involves tailoring treatments to individual patient needs, will necessitate adaptive GMP practices to ensure the quality and safety of these customized therapies. The ongoing evolution of GMP manufacturing promises to further enhance the efficacy and safety of pharmaceutical products, supporting better health outcomes worldwide.
Conclusion: The Critical Role of GMP in Pharmaceuticals
In summary, GMP manufacturing is indispensable in the pharmaceutical industry, ensuring that drugs are produced safely, effectively, and to the highest quality standards. This meticulous approach to production safeguards public health, fosters consumer trust, and reinforces the credibility of pharmaceutical companies. As the industry continues to advance and innovate, adherence to GMP guidelines will remain a cornerstone of pharmaceutical production, playing a vital role in enhancing global health and quality of life.
-
GENERAL2 months ago
Uncovering the World of кинокрадко: The Dark Side of Film Piracy
-
GENERAL1 month ago
Unveiling the Art of преводсч: How Translators Bridge Language Barriers
-
YOGA1 year ago
4 Person Yoga Poses for Beginners
-
GENERAL2 months ago
The Journey of iamnobody89757: From Anonymous User to Internet Sensation