GENERAL
Preventing Accidents: Top Safety Tips for Manufacturing Facilities
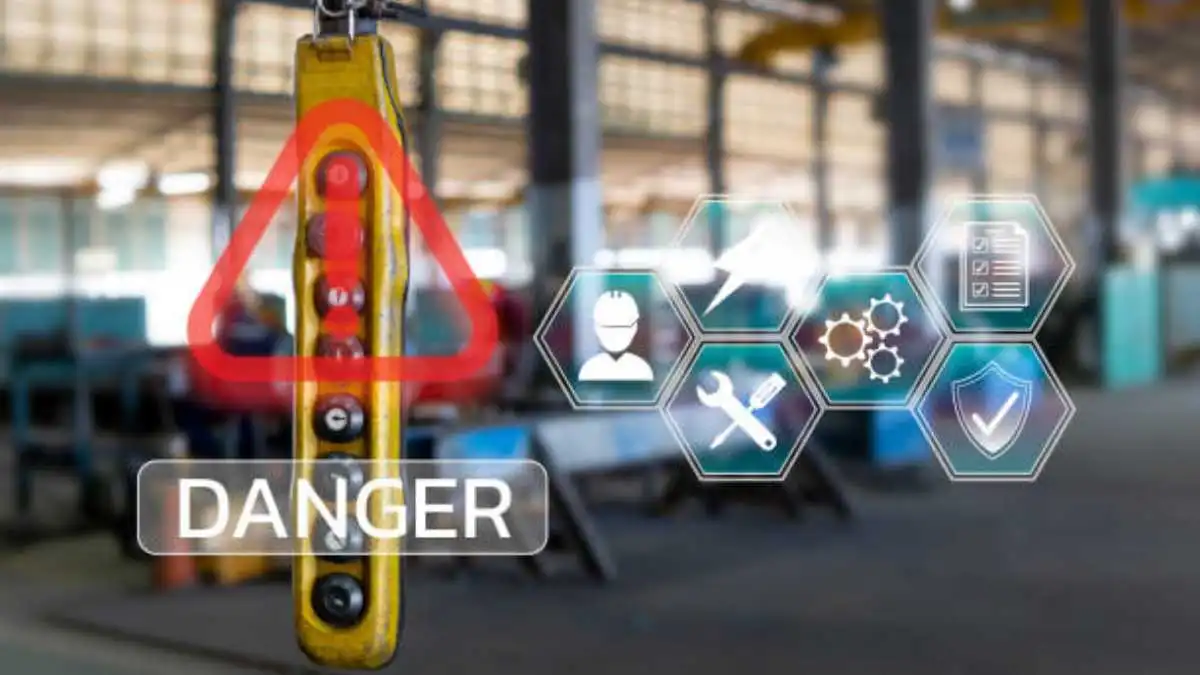
Manufacturing facilities are essential to various industries, from automotive to pharmaceuticals, but they also pose significant risks to workers. Heavy machinery, high temperatures, hazardous materials, and repetitive tasks can create dangerous work environments if safety protocols aren’t strictly followed. Preventing accidents should be a top priority for any facility to ensure worker well-being and operational efficiency. Here are some of the most effective safety tips to minimize risks and create a secure workplace.
Table of Contents
1. Implement Comprehensive Safety Training
One of the most effective ways to prevent accidents in a manufacturing facility is through thorough and ongoing safety training. Employees should be well-versed in the potential hazards of their job, including:
- Proper equipment handling
- Emergency response procedures
- Fire safety protocols
- The importance of personal protective equipment (PPE)
Regular refresher courses and practical demonstrations help reinforce safety practices, keeping workers alert and prepared. Additionally, new employees should undergo thorough onboarding that includes safety and environmental compliance training before they start working on the factory floor.
2. Enforce the Use of Personal Protective Equipment (PPE)
Personal protective equipment is the first line of defense against workplace injuries. Every manufacturing facility should enforce PPE usage based on specific job roles. Some essential PPE includes:
- Safety goggles to protect eyes from flying debris or chemical exposure
- Helmets to shield against falling objects
- Gloves for handling hazardous materials or sharp objects
- Ear protection in high-noise environments
- Respirators in areas with airborne contaminants
Supervisors should ensure that employees wear the correct PPE at all times and replace damaged or worn-out equipment immediately.
3. Maintain and Inspect Machinery Regularly
Faulty equipment is a leading cause of manufacturing accidents. Regular maintenance and inspections help identify issues before they lead to serious injuries. Companies should:
- Implement a preventive maintenance schedule
- Train employees to recognize early warning signs of equipment failure
- Conduct daily pre-shift equipment inspections
- Ensure that all safety guards and emergency shut-off switches function properly
If a machine shows signs of malfunction, it should be taken out of service until repaired to prevent potential hazards.
4. Keep Work Areas Clean and Organized
A cluttered work environment increases the risk of slips, trips, and falls. Proper housekeeping plays a critical role in workplace safety. Employers should enforce:
- Clear walkways and remove obstacles from high-traffic areas
- Proper storage of tools and raw materials to prevent falling hazards
- Regular cleaning of spills and debris, especially in slippery areas
- Designated areas for waste disposal to avoid buildup
By maintaining a clean workspace, companies can minimize preventable accidents.
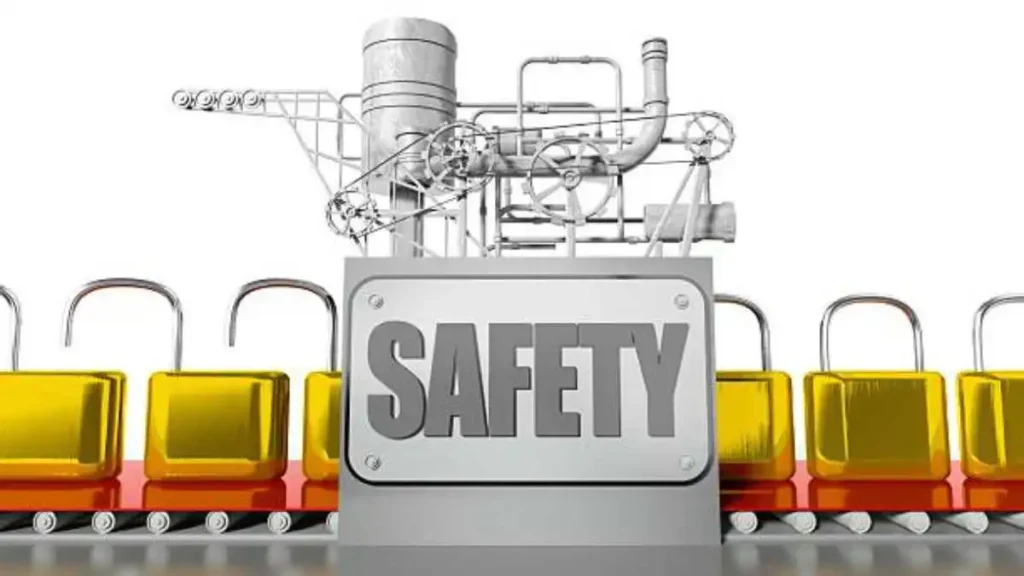
5. Establish Emergency Preparedness Plans
Accidents can still occur despite the best precautions, making emergency preparedness essential. Facilities should have well-defined response plans for fires, chemical spills, medical emergencies, and other workplace hazards. Key aspects of emergency preparedness include:
- Clearly marked exit routes and fire extinguishers
- Regular fire and evacuation drills
- First-aid training for employees
- Easily accessible emergency contact numbers
Having a structured plan ensures that employees know how to react quickly and effectively during an emergency, reducing the risk of injury and damage.
6. Promote a Safety-First Culture
Workplace safety isn’t just about rules—it’s about mindset. Companies that prioritize safety and create a culture where employees feel responsible for their well-being experience fewer accidents. This can be achieved by:
- Encouraging employees to report hazards without fear of retaliation
- Recognizing and rewarding safe work practices
- Providing open communication channels for safety concerns
- Involving employees in safety policy development
When safety becomes a shared responsibility, employees are more likely to follow protocols and take proactive measures to protect themselves and others.
7. Reduce Fatigue and Overexertion
Many workplace injuries occur due to worker fatigue or overexertion. Manufacturing jobs often require long hours and physically demanding tasks, leading to exhaustion and reduced attention to detail. Employers can address this by:
- Scheduling regular breaks
- Rotating tasks to prevent repetitive strain injuries
- Monitoring shift lengths to avoid overworking employees
- Encouraging hydration and healthy lifestyle habits
By prioritizing worker well-being, companies can enhance safety and overall productivity.
8. Use Signage and Safety Labels
Clear signage helps prevent accidents by alerting workers to potential hazards. Facilities should use:
- Brightly colored warning labels for hazardous materials
- Signs indicating restricted areas or machinery hazards
- Floor markings to define safe walkways and danger zones
- Instructions for proper machine operation
Effective signage ensures that workers are aware of dangers and can take precautions accordingly.
In Conclusion
Preventing accidents in manufacturing facilities requires a proactive approach, combining training, equipment maintenance, organization, and a strong safety culture. By prioritizing worker safety, businesses can reduce injuries, enhance productivity, and create a more secure working environment. Implementing these top safety tips can make all the difference in keeping employees safe and operations running smoothly.
-
GENERAL2 months ago
Uncovering the World of кинокрадко: The Dark Side of Film Piracy
-
GENERAL1 month ago
Unveiling the Art of преводсч: How Translators Bridge Language Barriers
-
YOGA1 year ago
4 Person Yoga Poses for Beginners
-
GENERAL3 weeks ago
Christofle – For Those Who Dream of Family Heirloom Silver