GENERAL
The Pros and Cons of Six Sigma vs Lean: Choosing the Right Methodology for Your Organization
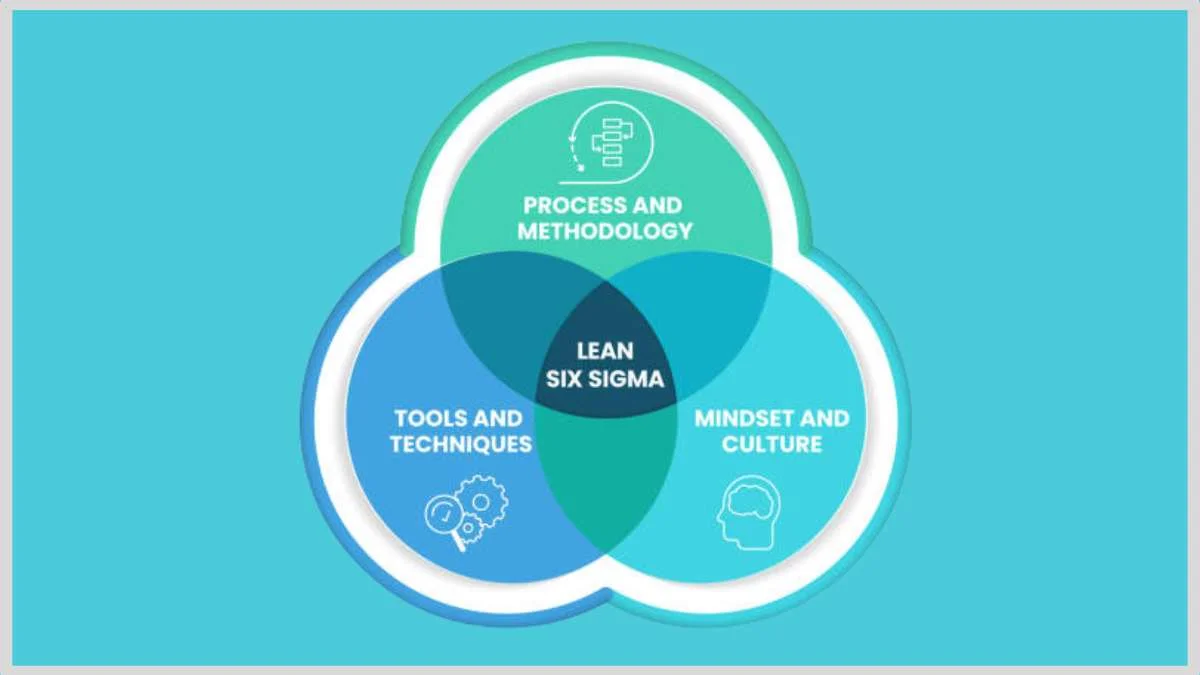
Are you struggling to decide between Six Sigma and Lean for your organization? You’re not alone. Many businesses face this dilemma as they try to improve their processes and increase efficiency.
Both Six Sigma and Lean are popular methodologies used in business process improvement. However, each approach has its own unique principles, tools, and techniques.
In this article, we will examine the pros and cons of Six Sigma vs Lean to help you determine which methodology is best suited for your organization.
Let’s dive in!
Table of Contents
What Is Six Sigma?
Six Sigma is a data-driven approach to process improvement that aims to reduce defects and variability in business processes. Motorola developed it in the 1980s. General Electric then popularized it.
Six Sigma uses statistical tools and techniques to identify and eliminate the root causes of problems. This methodology relies on a structured problem-solving approach known as DMAIC (Define, Measure, Analyze, Improve, and Control).
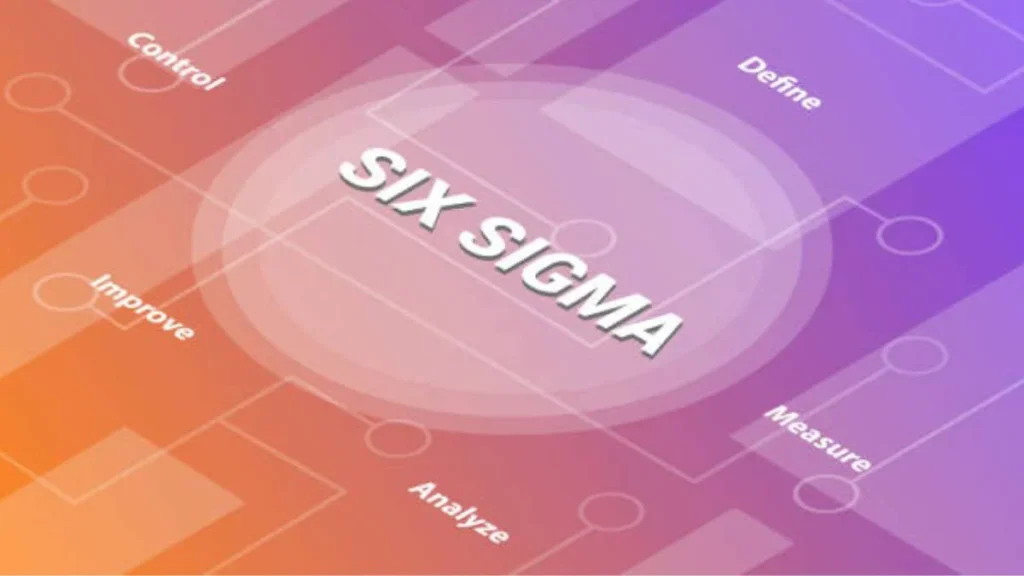
Pros of Six Sigma
Using Six Sigma can provide several benefits for your organization. This includes the following:
Data-Driven Decisions
Six Sigma emphasizes making decisions based on data and evidence rather than intuition or guesswork. This leads to more accurate and reliable outcomes.
Reduces Defects
By reducing defects and variability, Six Sigma helps organizations improve the quality of their products and services. This can lead to increased customer satisfaction and loyalty.
Continuous Improvement
Six Sigma is not a one-time initiative but a continuous improvement process. This ensures that processes are constantly monitored and improved, leading to sustained results over time.
Enhances Customer Satisfaction
Improved quality and consistency in products and services lead to higher customer satisfaction and loyalty. This can result in increased revenue and business growth.
Cons of Six Sigma
While there are many advantages to using Six Sigma, there are also some potential drawbacks to consider. These include:
Complex and Time-Consuming
Implementing Six Sigma can be a time-consuming process as it requires a thorough understanding and analysis of current processes. This may not be feasible for organizations with limited resources or tight deadlines.
High Costs
The costs associated with Six Sigma training and certification can be significant. This makes it less accessible for smaller organizations.
Heavy Focus on Data
While data-driven decisions are an advantage, the heavy reliance on data can sometimes overlook the importance of creativity and innovation. This may hinder the potential for new and innovative ideas.
Resistance to Change
Implementing Six Sigma often requires significant changes in processes and procedures. This can be met with resistance from employees. In the end, it’ll lead to delays or difficulties in implementation.
What Is Lean?
Lean is a methodology focused on maximizing value while minimizing waste. Originating from the Toyota Production System, Lean aims to:
- Identify and eliminate waste
- Continuously improve processes
- Empower employees to make decisions
Lean emphasizes creating efficient and streamlined processes to meet customer demand with minimal resources. Popular tools used in Lean include:
- Value Stream Mapping
- 5S
- Kanban
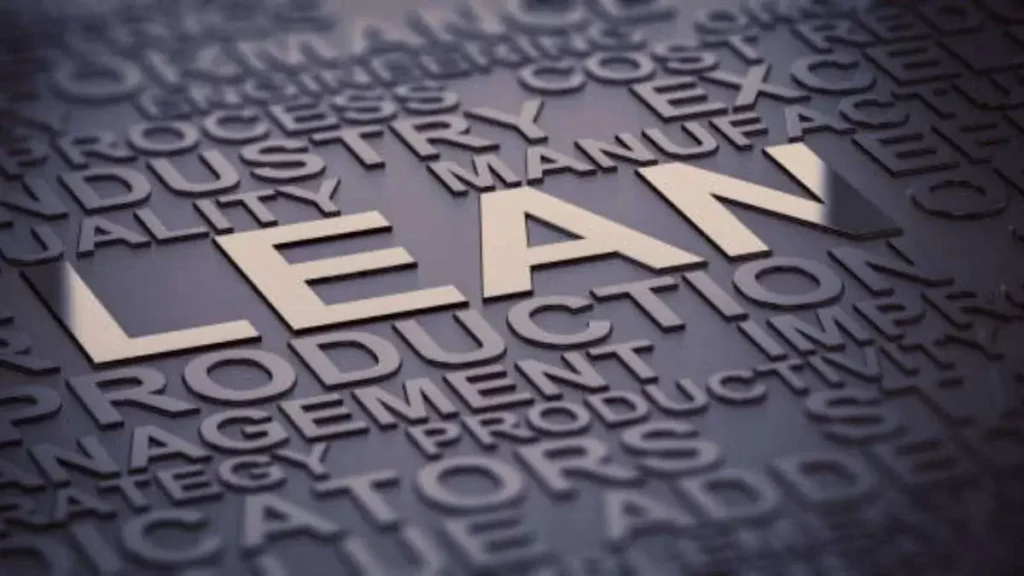
Pros of Lean
Implementing Lean can bring various benefits to an organization, including:
Simplifies Processes
Lean emphasizes simplicity and streamlining processes. This makes it easier to implement and understand. It also helps reduce the chances of errors and delays.
Eliminates Waste
Lean identifies and eliminates waste in processes, leading to increased efficiency and cost savings. This can result in improved profitability for organizations.
Improves Employee Engagement
Lean encourages employee involvement and empowerment. This fosters a culture of continuous improvement and collaboration. It can also lead to increased morale and job satisfaction.
Focuses on Customer Value
By focusing on value from the customer’s perspective, Lean ensures that processes are aligned with customer needs and expectations. This leads to improved customer satisfaction.
Cons of Lean
While Lean has many advantages, there are also some potential downsides to consider:
May Overlook Quality
While Lean focuses on efficiency and waste reduction, it may sometimes overlook the importance of quality and defect reduction. This can lead to decreased customer satisfaction and loyalty.
Requires Cultural Change
Implementing Lean often requires a significant cultural shift. This can be challenging for some organizations. It also takes time and effort to fully embed Lean principles into an organization’s culture.
Limited Use
Lean is primarily used in manufacturing and production environments. This may not be suitable for service-based organizations or those with complex processes.
Six Sigma vs Lean: Key Differences
To make an informed decision, it’s essential to understand the key differences between Six Sigma and Lean.
Focus
Both approaches aim to improve quality, but their primary focus differs. Six Sigma focuses primarily on reducing defects and variability. Meanwhile, Lean emphasizes eliminating waste and improving efficiency.
Approach
Six Sigma uses a data-driven, statistical approach to problem-solving. Lean, on the other hand, relies on straightforward principles and visual management techniques.
Tools and Techniques
Six Sigma employs various statistical tools and techniques, such as DMAIC (Define, Measure, Analyze, Improve, Control). Meanwhile, Lean uses tools like Value Stream Mapping and 5S (Sort, Set in order, Shine, Standardize, and Sustain).
Integrating Six Sigma and Lean: Lean Six Sigma
For organizations seeking the best of both worlds, Lean Six Sigma combines the strengths of both business methodologies. Lean Six Sigma aims to improve efficiency and quality by eliminating waste and reducing defects.
Pros of Lean Six Sigma
Using the integrated approach of Lean Six Sigma can bring numerous benefits. These include:
Comprehensive Approach
Lean Six Sigma offers a comprehensive approach to process improvement. It addresses both efficiency and quality, leading to improved overall performance.
Enhanced Problem-Solving
By integrating Lean and Six Sigma, organizations can leverage a broader range of tools and techniques for problem-solving. This leads to more effective and efficient solutions.
Greater Flexibility
Lean Six Sigma provides greater flexibility. It allows organizations to tailor their approach based on specific needs and goals. This can be useful for organizations with diverse processes.
Cons of Lean Six Sigma
While Lean Six Sigma offers many advantages, it also has some potential drawbacks:
Complexity
Combining two methodologies can increase complexity. It may require more extensive training and resources.
Potential Conflicts
Integrating Lean and Six Sigma may lead to potential conflicts, as the methodologies have different focuses and approaches.
Choosing the Right Methodology for Your Organization
When deciding between Six Sigma and Lean, it’s essential to consider some factors. These include:
Organizational Goals
Identify your organization’s primary goals and objectives. Are you looking to improve quality? Do you want to reduce defects? Or maybe you want to enhance efficiency?
Understanding your goals will help you choose the correct methodology. For example, Six Sigma might be the better option if you’re primarily concerned with reducing defects.
Resources
Consider the resources available for implementation, including:
- Time
- Budget
- Personnel
Six Sigma may require more extensive training and resources. Meanwhile, Lean may be more accessible for smaller organizations.
Cultural Fit
Assess your organization’s culture and readiness for change. Implementing Lean may require a cultural shift. Meanwhile, Six Sigma’s data-driven approach may be more suitable for data-centric organizations.
Industry
Consider the industry in which your organization operates. Some industries may benefit more from Six Sigma’s focus on quality and defect reduction. Meanwhile, others may find Lean’s emphasis on efficiency better.
Complexity of Processes
The complexity of your organization’s processes should also be a factor in choosing the methodology. Lean may not be suitable for highly complex processes. Six Sigma’s statistical tools, on the other hand, can handle more complicated data.
Implementing Your Chosen Methodology
Once you have chosen the right methodology for your organization, it’s time to implement it. You must:
Plan and Prepare
Before implementing Six Sigma or Lean, develop a detailed plan outlining the required steps, resources, and timeline. Ensure you have the necessary support, training, and infrastructure to support the implementation process.
Engage Stakeholders
Engage key stakeholders. This may include:
- Employees
- Management
- Customers
Ensure they understand the benefits and objectives of the chosen methodology. This will help gain buy-in and support for the implementation.
Provide Training and Support
Proper training and support for employees at all levels will help ensure a smooth transition and increase the chances of success.
Both Six Sigma and Lean require a thorough understanding of the principles and tools to be effective.
Meanwhile, for Lean Six Sigma implementation, consider checking out these resources at https://www.theleansixsigmacompany.co.uk/green-belt-course/.
Monitor and Evaluate
Regularly monitor and review the implementation process. This will help identify any issues or areas for improvement. Make adjustments as needed to ensure a successful outcome.
Celebrate Successes
Don’t forget to celebrate successes. Recognize and reward individuals and teams for their contributions to the implementation process. This will help maintain motivation and engagement.
Exploring the Pros and Cons of Six Sigma vs Lean Methodologies
Understanding the pros and cons of Six Sigma vs Lean is essential so you can choose the most suitable methodology for your needs. You can also consider integrating Lean and Six Sigma for a more comprehensive approach.
With careful planning, implementation, and continuous improvement, your organization can achieve sustained success through process improvement. So don’t wait any longer! Start implementing Six Sigma or Lean in your organization today!
Was this article helpful? If so, check out the rest of our site for more informative content.
-
GENERAL2 weeks ago
Christofle – For Those Who Dream of Family Heirloom Silver
-
GENERAL2 months ago
Uncovering the World of кинокрадко: The Dark Side of Film Piracy
-
GENERAL4 weeks ago
Unveiling the Art of преводсч: How Translators Bridge Language Barriers
-
SPORTS2 months ago
Discover the World of Football with Streameast: Watch Your Favorite Leagues and Tournaments