GENERAL
What is a Pneumatic Cylinder? Understanding Its Role in Automation
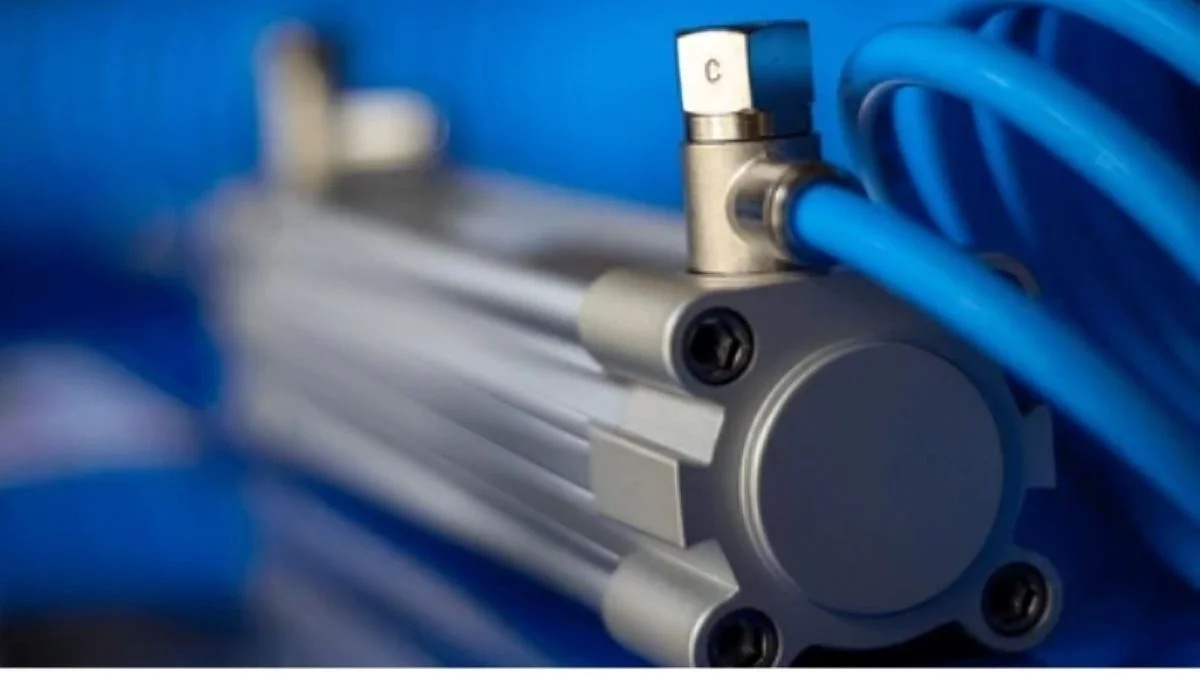
Industrial automation would be difficult to achieve without well-designed pneumatic cylinders, as they ensure precise motion control for many processes. These devices change mechanical energy into compressed air for storage and use in automation systems. The air can be utilized for lifting, pushing, pulling, and even rotating some objects. As industries move towards more automation, partnering with an industrial automation solution provider becomes essential to proper integration and optimization of pneumatic cylinders and other components of the system. In this article, we will discuss what a pneumatic cylinder is, its components, how it works, and how it contributes to modern automation. Pneumatic cylinders are a common form of inexpensive actuators used in different automation environments because of their simplicity and functionality. A greatest feature of pneumatic cylinders is the ability to improve industrial functionality without sophisticated electrical or hydraulic systems. This greatly increases productivity of different industrial tasks.
Table of Contents
What is a Pneumatic Cylinder?
A Pneumatic Cylinder is a device that is capable of actuating linear movements through the utilization of compressed air. It is made from a piston, rod and cylinder, which work in response to the increase or decrease of air pressure. Pneumatic cylinders operate with the basic principle of air expanding and contracting within the cylinder. Because of this, the motion is either linear or rotational. They are quite popular in the fields of production, automotive, robotics, and packaging. It is due to their ease of applicability and efficiency that they are so popular. These cylinders, when combined with an industrial automation solution, increase efficiency through lowering manual tasks, increasing accuracy, and speeding up automated processes. Their wide adaptation range also allows them to be used in extreme conditions, ensuring their place in the automation of today’s world. The adoption of these devices in other industries also continues to rise as the demand for efficient and stricter solutions become commonplace. From standalone solutions to complex challenges, customization guarantees their importance for modern automation.
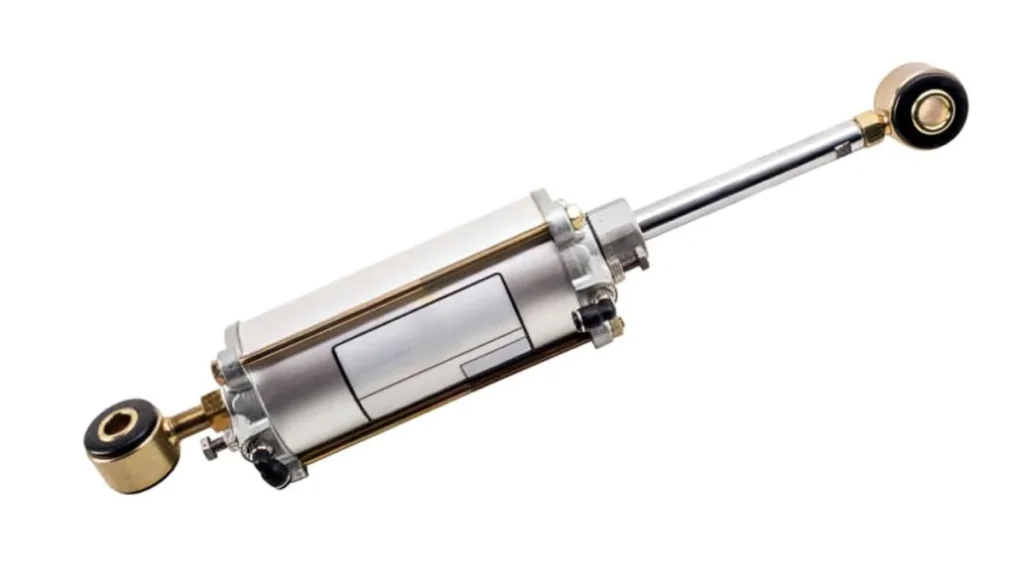
How Does a Pneumatic Cylinder Work?
A pneumatic cylinder’s operation is based on controlled use of compressed air. To better understand a pneumatic cylinder and its mode of operation, let us analyze its mechanism. The process starts with compressed air being fed into one end of the cylinder through an inlet. The pressure generated pushes the piston, which extends the piston rod. At the same time, the air behind the piston is released using an outlet port. The piston exerts a force on the rod which is in the cylinder. When the piston moves to the maximum stroke position, the direction of air flow is reversed. As a result, the piston moves back to the starting position and the rod is pulled back. The system comprising the pneumatic cylinder and valves is usually referred to as a pneumatic system. The piston will be in the middle position at rest. The supplied air pressure will determine the position of the piston. A spring will return the piston to the neutral position if no air is applied. Air can be fed alternately , which can push the piston both from the front and behind the piston. With almost no limitation, the speed and force of the this cylinder can be adjusted due to the regulation of air supply pressure and flow rate. This gives a pneumatic cylinder flexibility in automated instructions.
Real-time monitoring and feedback are possible with the help of sensors, which can adjust parameters like speed and force. This helps to enhance the performance of modern pneumatic systems, which are designed with smart control features. As a result, pneumatic cylinders are versatile and can be used effectively in many different applications.
Styles of Pneumatic Cylinders and How they are Used
The types of pneumatic cylinders differ with each other to some extent in their designs as well as in their applications. Single acting pneumatic cylinders are designed to handle the compressed air in only one direction. This mechanism is best suited for basic applications where only a limited and very low motion is necessary. Pneumatic double acting cylinders use air in the piston space above and below the piston enabling controlled movement in both directions. Their extensive use in industrial automation is due to their efficiency in a wide range of applications. Rodless cylinders utilize space more effectively as there is no piston rod. Instead, a mechanical linkage or magnetic coupling moves the load. Rotary pneumatic cylinders change linear motion to rotary motion. These cylinders find application in turning and indexing. Telescopic cylinders extend through multiple stages providing longer strokes while retaining tighter dimensions. The unique stroke capability makes them very suitable for applications with limited available space. Choosing the correct type of pneumatic cylinder depends on stroke length, load weight, and motion speed for effective functionality in automated systems.
With the changing requirements for automation, the technology of pneumatic cylinders continues to solve problems for more complicated tasks and systems.
Advantages of Pneumatic Cylinder Usage in Automation Work
The use of pneumatic cylinders in the field of automation comes with a lot of advantages. First off, these advantages include cost-effectiveness and simplicity, which tend to benefit people the most. Unlike electric or hydraulic devices, pneumatic ones possess a reduced number of moving parts that favor reliability and low maintenance needs throughout its service life. Such affordable devices provide a solution for businesses looking to automate processes without significant investment. Efficient use of energy is an additional advantage as process air is very accessible and can be adjusted to suit needs. It operate at high speeds, resulting in faster response times and improved production rates. Their ability to function in hazardous environments is an additional factor to consider as they do not generate sparks, which makes them useful for food processing, pharmaceutical, and chemical manufacturing industries. Moreover, they can be tailored to fit conveyor systems and robotic arms and most installations are flexible. In order to fully exploit the benefit of pneumatic cylinders, the correct application engineering is paramount. Adoption of industrial automation is ever-growing, and so is the use of pneumatic devices, their minimal nature is what makes them an essential component in achieving high productivity systems.
Being able to operate in extreme heat or moist environments make them extremely useful in diverse industries.
Conclusion
Pneumatic cylinder is a necessary element of industrial robotics as it provides accurate, efficient, and economical movement management. Knowing what a pneumatic cylinder is and how to use it ensures that the right type of cylinder is selected. Different types of cylinders, such as single-acting, double-acting, rodless, and rotary cylinders, allow businesses to select a cylinder that will best serve to optimize their automation systems. Balance of cost, reliability, and efficiency makes pneumatic cylinders critical parts of contemporary automated systems. The fast-changing nature of industries means that the need for robust pneumatic technologies will always be there, fostering innovation and increased efficiency of automated systems. Smooth operation, minimal downtime, and considerable savings of resources in the long term make investing in quality pneumatic cylinders prudent in any industrial automation environment. By advancing the technology of cylinders and control systems, corporations may exploit the full capabilities of their pneumatic based automation systems, ensuring high standards of sustainability and efficiency in the manufacturing processes. Early adopters of modern pneumatic automation will be able to enjoy the competitive due to high precision, lower costs of operation, and greater productivity.
Want more tips? Visit our blog for valuable insights and resources!
-
GENERAL2 months ago
Uncovering the World of кинокрадко: The Dark Side of Film Piracy
-
GENERAL1 month ago
Unveiling the Art of преводсч: How Translators Bridge Language Barriers
-
YOGA1 year ago
4 Person Yoga Poses for Beginners
-
GENERAL3 weeks ago
Christofle – For Those Who Dream of Family Heirloom Silver